The Digital Construction Awards attracted 170-plus entries this year, 85 of which have been shortlisted. Here, we detail the finalists for Best Application of Technology.
This category recognises the most effective application of a specific existing technology. Existing means a product (hardware or software) that has been available on the market for more than 18 months.
This category was overwhelmed with excellent entries, so there are 11 nominations.
Arup’s Fuse, with its AI engine ProjectGPT, is an intelligent project portal that unifies project data, apps and teams, revolutionising Arup’s approach to digital design and construction.
Fuse connects and visualises project data, saving time and money while enabling better decision-making. It features configurable apps and centralised user management under a single URL. It integrates various data forms, including geographic information, spatial analysis, risk registers, 3D models and point clouds. The platform also connects with existing apps and data stores like SharePoint, ProjectWise and BIM360, minimising disruption to workflows.
With more than 145 active projects across the world, it has saved the business 1,500 hours in just three months. The integration of ProjectGPT across project data within Fuse has transformed how Arup handles massive amounts of project documentation. By using AI to understand and generate human language, it enables Arup teams to find and summarise information quickly and accurately. This has reduced errors and freed up Arup teams to focus on delivering.
Arup is working for the Canadian transport agency, Metrolinx, whose director Nasir Qureshi said: “Fuse really brought our teams together, with a lot of innovative ideas in terms of how to record and track the construction progress. Where teams are working remotely in different locations, this tool really helps us to stay connected to the day-to-day progress of the project.”
Automating assurance: a data-driven transformation to deliver complex assurance efficiently | Laminar Projects
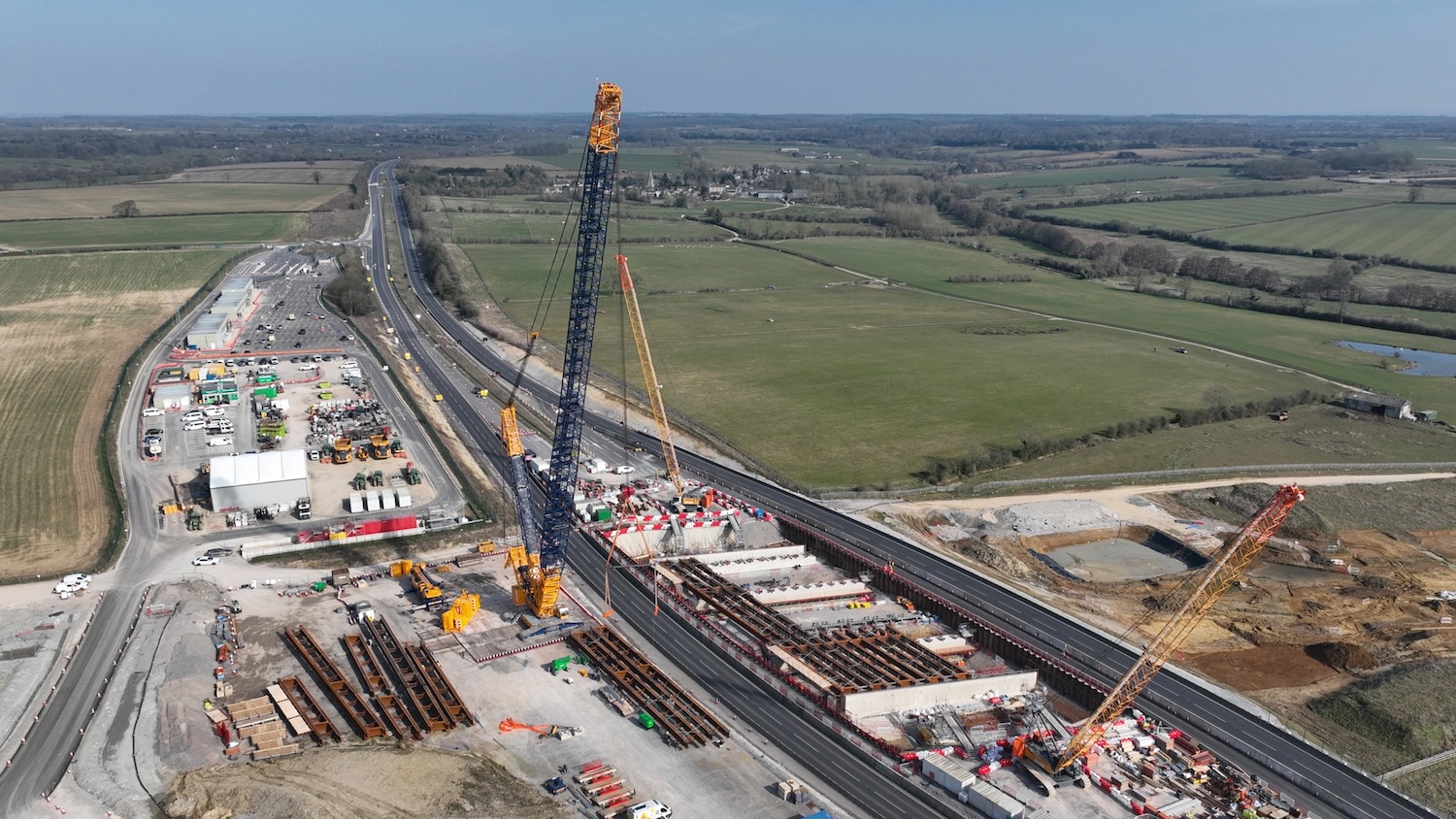
Laminar Projects has transformed the EKFB (Eiffage, Kier, Ferrovial Construction BAM Nuttall) JV’s data acceptance certificate (DAC) process, ensuring asset information meets standards set by EKFB’s client, HS2.
Despite its potential to enable the golden thread, the DAC was seen as a major blocker to project progress, due to delays resulting from challenges across the process, including complex data collection, lengthy validation and inconsistent feedback to EKFB’s subcontractors.
Laminar’s solution leveraged Microsoft’s advanced functionality, creating a streamlined ecosystem that integrates with existing software, which is a significant step-change over semi-manual methods and point solutions typically used. The connected ecosystem delivered significant efficiencies through automation of checks, real-time data and enhanced communication across teams.
- increased compliance: 92% of DACs were fully accepted by HS2 in 2025, compared with 3% in 2023;
- increased efficiency: reduced re-submission time by 36% (22 days to 14 days) by enabling comprehensive, automatic communication of errors;
- time savings: compiling a DAC was reduced from 4.5 hours to 2 hours (55%); and DAC checking from 45 minutes to 15 minutes (66%);
- faster onboarding is enabled as requirements built into the PowerApp and dashboards guide the user; and
- live data updates ensure compliance until submission, with new ISO 19650 revisions identified across multiple partner organisations’ CDEs.
Electricity transmission substation site visits | AtkinsRéalis
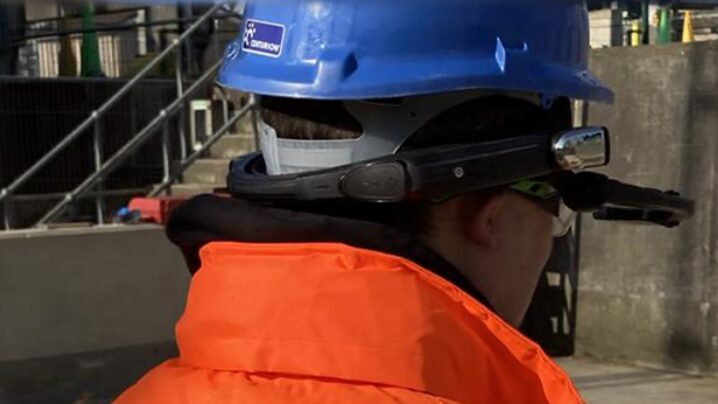
Significant volumes of substations and network upgrades are required to achieve net-zero targets efficiently and cost-effectively. AtkinsRéalis’s design process involves visiting substations to gather onsite details to develop appropriate solutions.
However, this approach comes with several challenges, including health and safety considerations around electrical risks of substations, remote locations requiring overnight stays, difficulties in interpreting 1960s hand-drawn as-built drawings, and discussions with stakeholders who have never visited the site, among other issues.
To overcome these obstacles, AtkinsRéalis identified two technologies, namely the GoPro MAX camera, which captures 360-degree photos and videos, and the RealWear Navigator assisted reality headset.
During previous site visits, teams captured photographs and videos using mobile phones, creating large datasets that lacked broader context, including only specific site sections within each frame, making them difficult to refer to later.
AtkinsRéalis trialled GoPro MAX devices on standard substation visits. A camera attached to a worker’s helmet allowed hands-free data capture, leaving them to focus on the visit and hazards. Initial users were substation engineering SMEs, which had to prioritise site engineering assessments, rather than optimally capturing suitable footage.
While 360-degree footage creates valuable ‘virtual sites’, it does not facilitate live contributions from those not on site. However, RealWear Navigator enables livestreams from the wearer’s perspective to Microsoft Teams, allowing users to attend the site virtually, and all participants can interact while referring to the livestreams.
The deployment of this digital technology has improved the way projects are delivered and created new methods of communicating and optimising design development.
Improving access to the UK BIM Framework Guidance | nima/Morta
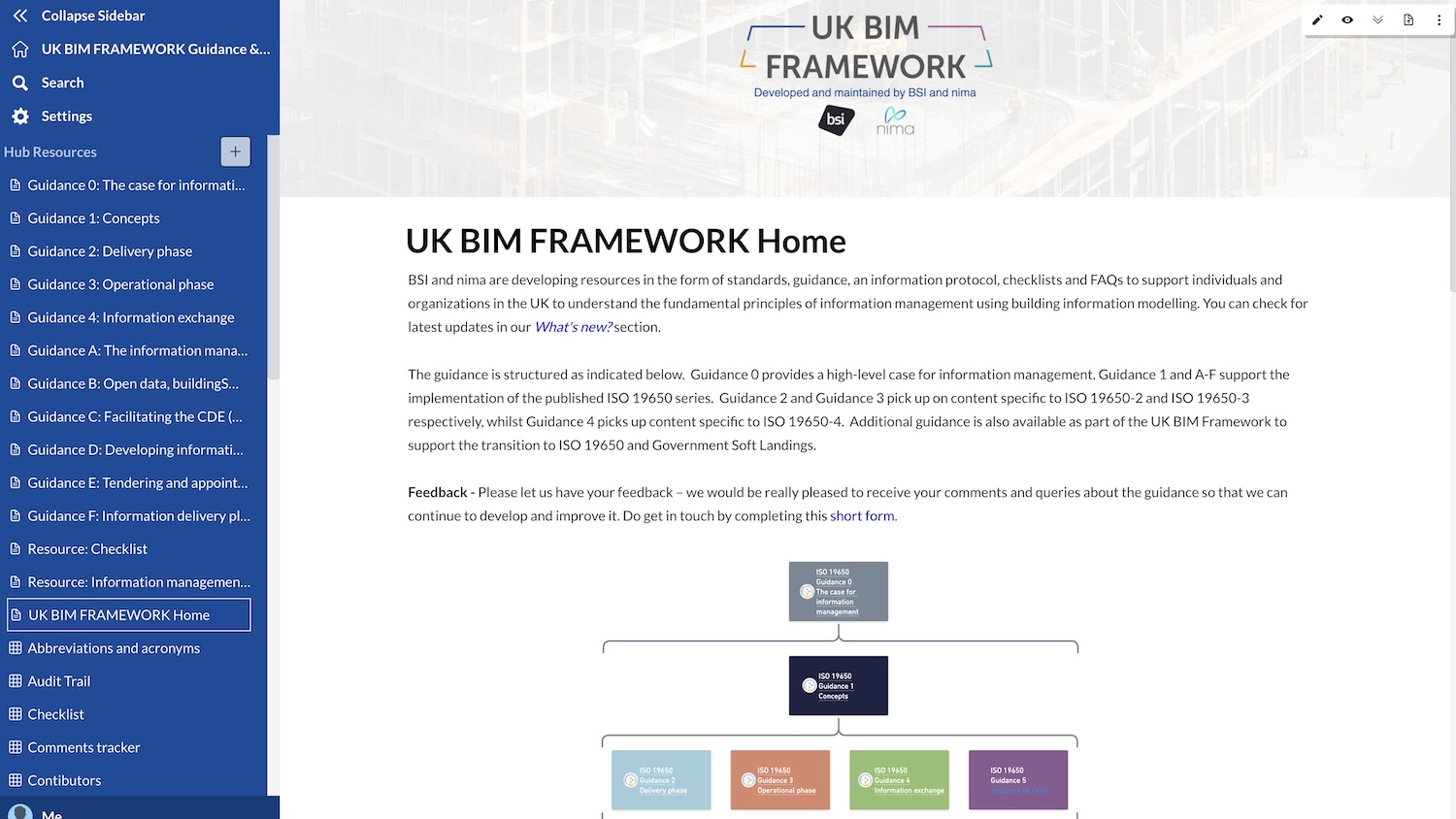
The UK BIM Framework Guidance website is the only curated, maintained and reliable insight for implementation of the UK BIM Framework. It hosts more than 350 pages and 100,000 words.
Before implementing Morta-AI, users downloaded static PDFs of the guidance, which would go out of date. Developments led to the use of Airtable and Notion to provide online access to the guidance. This improved reliability of content, but presented usability challenges with content being on two different platforms. Full capability could not be leveraged without moving to paid plans: an unviable move for a community-based resource.
In addition, the rise of AI search tools led to outdated or inaccurate answers to questions, for example, referencing outdated standards like PAS 1192-2. This presented risks to the industry, as misinformation could lead to non-compliant and inefficient workflows.
To address this, the UK BIM Framework team sought a dynamic, web-based solution to combine the best of Word and Excel with the structured properties of a database. The goal was to create a connected, interactive, and AI-enabled platform to improve accessibility and lay the foundation for future tools to enhance industry collaboration and digital adoption.
A small team of volunteers from nima worked with Morta to transition the guidance content onto the Morta platform and develop the user experience and the user interface. Morta brought new features not available in the previous guidance platform, including an AI search function, which has revolutionised how users can interact with the guidance to get answers to real-world questions.
The Morta platform also gives nima access to live, detailed data about how the guidance is being accessed and used. With this, nima can understand where strategic development of the guidance is needed.
Improving construction sequencing on infrastructure projects | Skanska and Esri ArcGIS
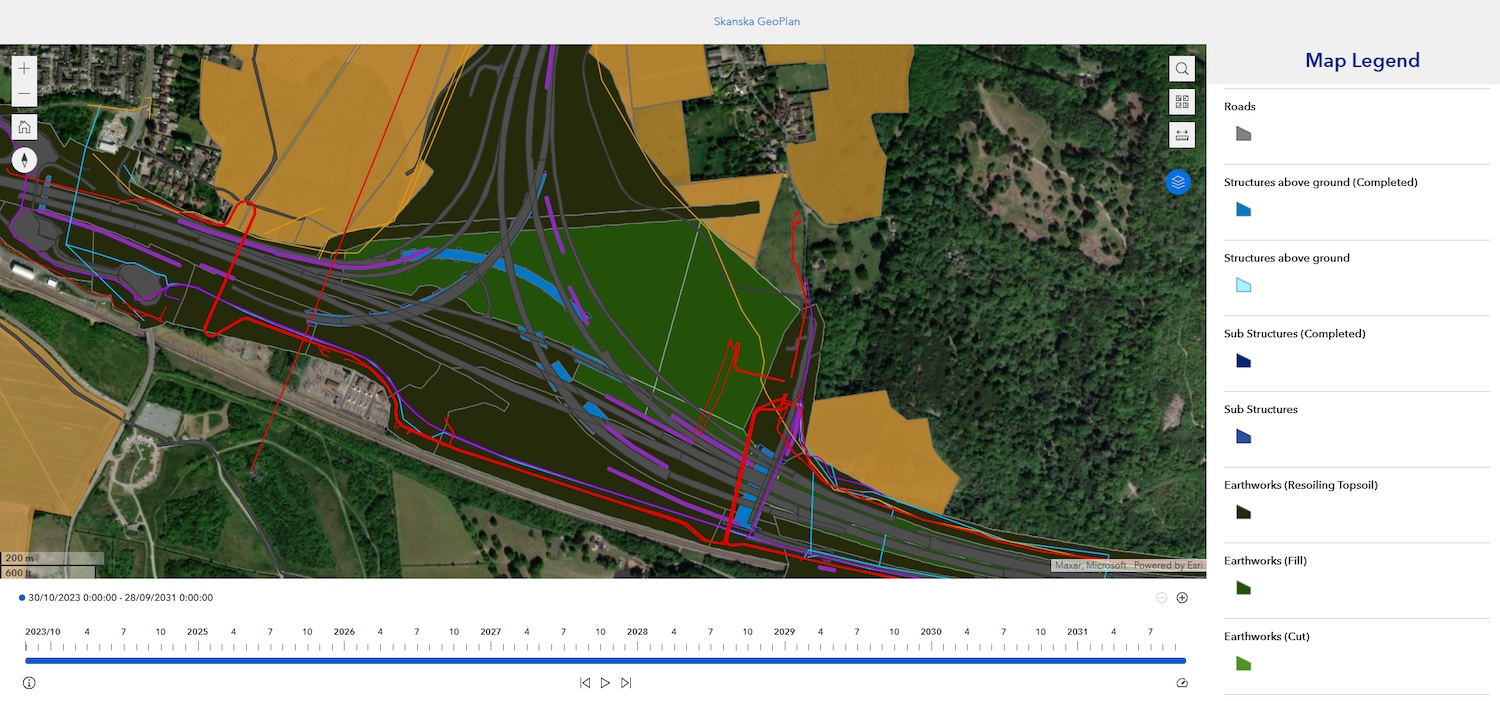
By replacing a lengthy manual process with a new streamlined workflow, Skanska has revolutionised the planning and sequencing of construction projects, delivering significant value to clients.
Using ArcGIS geospatial technology from Esri UK, Skanska developed a digital rehearsal process and a collaborative planning environment, called Skanska GeoPlan, which incorporates spatial context. This allows project teams to scrutinise and interrogate programmes in a digital setting, improving comprehension of project constraints, risks and logistical challenges during programme development. Consequently, this leads to improved project delivery and cost reductions.
Skanska GeoPlan is hosted on Skanska’s Esri ArcGIS Enterprise platform, enabling the sharing of geospatial construction sequences with non-technical colleagues in an intuitive, interactive, map-based environment far more efficiently than before.
Claire Lepoutre, infrastructure technical services director at Skanska, highlighted the ease of adoption: “The beauty of Skanska GeoPlan is that it uses existing tools our teams are comfortable with in a novel way. Engagement with the original project team was quick; interest has rapidly spread across our projects. It is simple to use, engage with and modify and is now firmly part of our digital rehearsal tools suite.”
Over the past year, Skanska has implemented Skanska GeoPlan on the Lower Thames Crossing project, facilitating the onboarding of new team members as construction gears up. The system enables digital rehearsals for the various interconnected phases, achieving a time saving of 10 months on this project alone.
Deliverables Review Platform | Mace
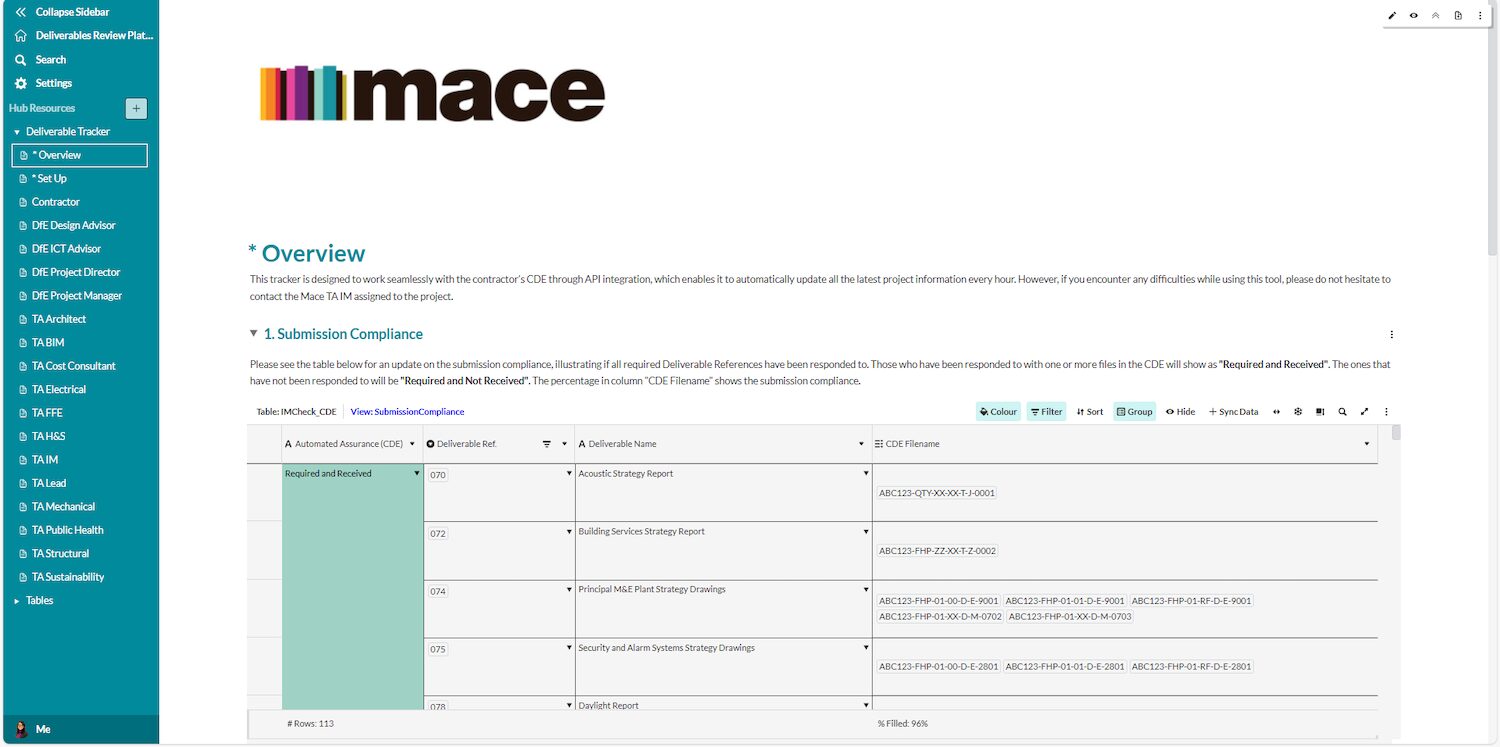
With the then-information management mandate, Mace’s technical advisory teams faced the challenge of reviewing deliverables across multiple common data environment (CDE) solutions. This led to significant pushback due to the need for training on various platforms, a common hurdle when introducing new systems. To overcome this, Mace developed a centralised solution that streamlined the review process.
Mace’s Deliverables Review Platform, developed for the Department for Education (DfE) Construction Framework 2021, embodies the essence of a CDE as an interconnected ecosystem rather than a single solution. By bridging the gap between different systems, Mace accommodated the DfE’s constraints, which prevent it from requiring a single CDE solution for hosting project information. Instead, Mace turned this challenge into an opportunity by creating a solution that leverages structured information.
Mace saw potential in Morta’s one-click integrations, which enable secure synchronisation to CDE solutions via APIs. This allowed Mace to maintain the integrity of information within the project’s CDE solution while providing accurate and up-to-date reports on the delivery team’s submissions.
Mace ran an initial trial on three projects, and by April 2024, the Deliverables Review Platform was rolled out across the sector, with 25 active projects as of March 2025. Pursuing an agile implementation, Mace took feedback from each project team and refined the template to benefit future projects. Framework-wide and project-specific training sessions were arranged and recorded.
Additional functionalities included notifications, unique reference numbers for comment threads, allowing the technical adviser lead to amend the reviewer matrix for project-specific requirements, and giving the delivery team a preview of Mace’s information management compliance to address non-compliances early on.
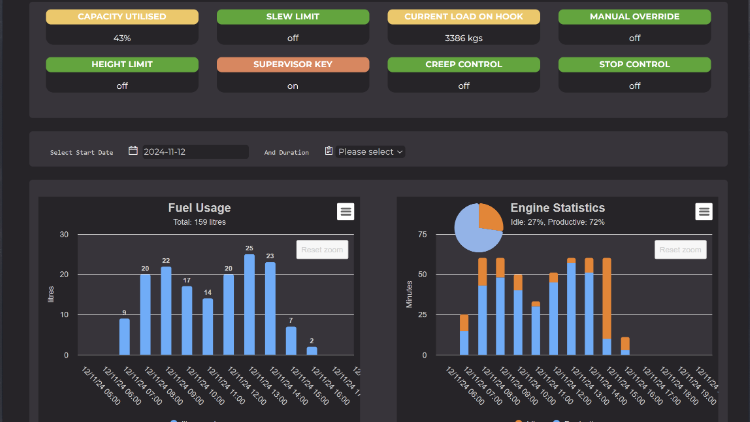
PVS Data saw a need to enable construction sites operating a mixed fleet of plant to view telematics data through one platform rather than myriad brand-specific ones.
PVS wanted to create a solution that could not only be adopted by a site manager working with the machines and operators on the ground, but also the auditor in the office looking for ISO 15143-3 data.
12 months of development later, PVS Data had produced a plugin unit and platform that work hand-in-hand to provide real-time, actionable data for users on site and in offices. Providing a machine has one of PVS’s D2 units installed, users can see every machine in their fleet, including:
- its location down to a 3m x 3m square;
- the fuel it has used within a customisable time frame;
- exact machine hours;
- the machine operator’s climate;
- keycodes that have been used to try to mobilise the machine; and
- up to another 295 parameters.
The details of each machine are each laid out in the same way, producing the same live information for the entire construction fleet.
The platform includes a service dashboard, ensuring plant hirers and users can adhere to service intervals. A machine fault dashboard has proved invaluable in reducing downtime of machines and paid operators, in effect, pre-warning the users before the machine goes down.
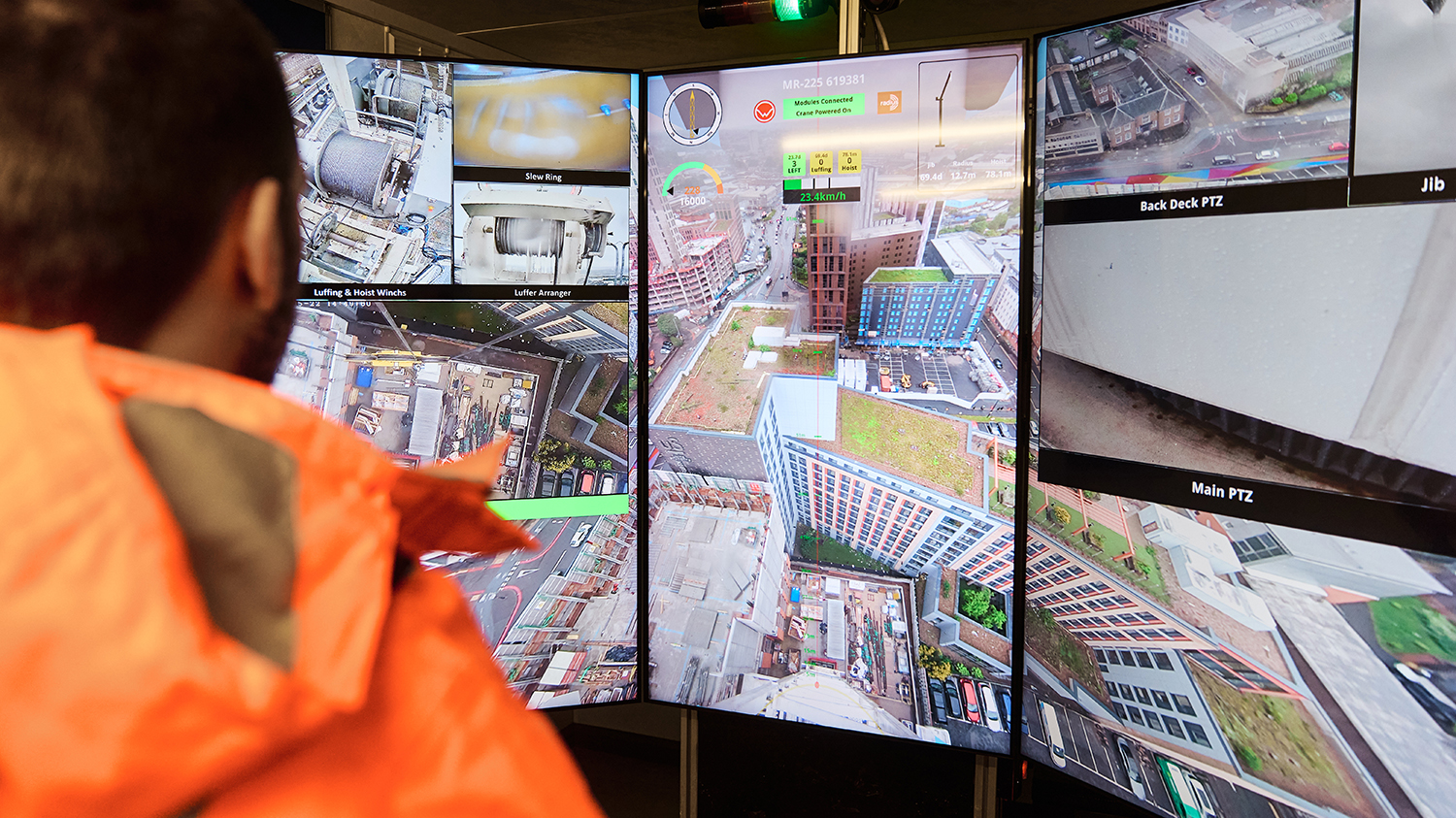
Traditionally, tower crane operators sit dozens of metres in the air, battling limited visibility, unpredictable weather and high-risk conditions. Skyline Cockpit flips that on its head.
With a multi-angle camera system, operators get a panoramic view from the ground of every essential angle: from the trolley winch to the hook-and-load line, eliminating the need to squint through a tiny window.
Skyline Cockpit’s cutting-edge software stitches visuals into a single, intuitive display, layering in augmented reality to anticipate exact landing spots in real-time. Real-time alerts, safety warnings and weather-based adjustments turn crane operation from guesswork into precision.
The system can be retrofitted to existing tower cranes. Unlike fully automated solutions that require new machinery, Skyline Cockpit upgrades traditional cranes, making remote operation accessible without massive capital investment. It also allows one operator to manage multiple cranes, addressing the labour shortage without impacting efficiency.
Skyline Cockpit’s first UK deployment took place in partnership with Winvic and Radius Group at the Crown Place Birmingham project, a 33-storey student accommodation development.
The process came with challenges, including crane operators being initially sceptical about moving from the cab to the ground and regulatory compliance (remote operation in a live construction site required close collaboration with site safety teams). However, once the crane operators experienced the improved visibility, ergonomic set-up and reduced fatigue, adoption accelerated.
Skyline Cockpit also worked alongside Winvic to ensure seamless integration with existing workflows to ensure regulatory compliance.
After a 12-week trial, Winvic kept the system on site, reporting a 10% increase in crane efficiency.
Transforming information delivery planning | Tilbury Douglas/Asite
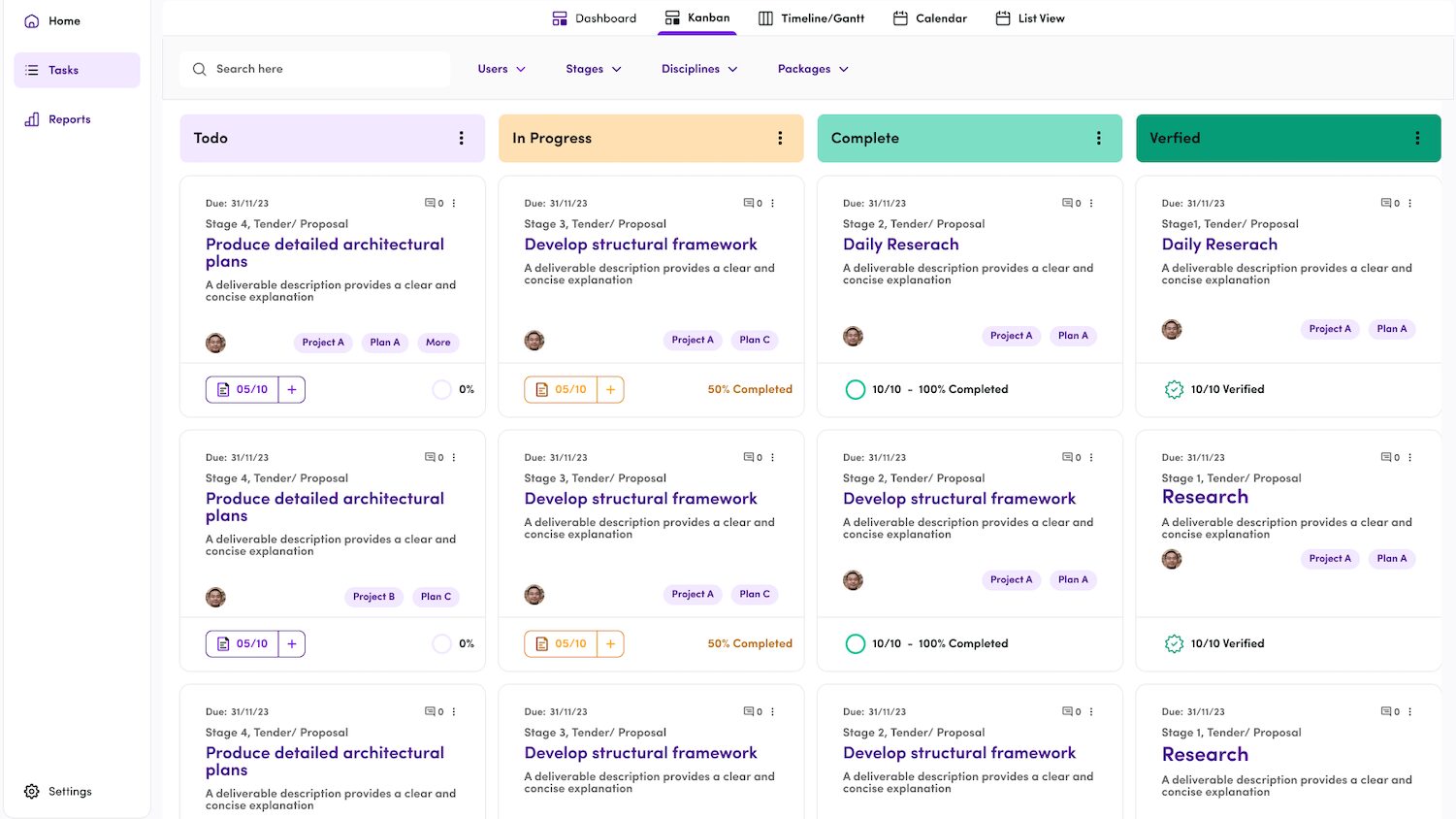
Following a company-wide audit, Tilbury Douglas identified key areas for improvement: operational efficiencies, communication, supply chain management, digital security and sustainability. It also aimed to add value for clients through advanced digital information management.
Tilbury Douglas sought an intuitive tool to manage work packages, tasks, and deliverables across 400 projects internationally. With more than 1,000 suppliers and a £2bn construction value, it required an integrated management system (IMS) aligned with the UK BIM Framework and ISO 19650 standards. Finding no existing tool that met its stringent requirements, Tilbury Douglas partnered with Asite to develop a bespoke solution.
Following nine months of development, Tilbury Douglas now has an IMS that automates the tracking of information deliverables at both project and organisational levels. Previously managed on Excel spreadsheets, progress reporting is now automated, eliminating outdated reports and ensuring real-time accuracy. It extracts actionable reports from the CDE, displaying information plans scalable from project to organisation level.
The IMS empowers contributors to understand their tasks and gives project and information managers a data-driven view of deliverables. This fosters greater transparency and accountability across our projects. To ease adoption, familiar tools like Kanban boards and Gantt charts were incorporated, ensuring an easier transition for teams.
A total of 1,200 staff, contractors and supply chain partners have been trained on the IMS.
- 100% reduction in back-and-forth emails for document tracking, eliminating inefficiencies;
- 1,500 hours saved per project on paperwork and communication; and
- £75,000 cost savings per project.
Water Industry Printfrastructure | United Utilities/Scottish Water/Manchester Metropolitan University/ChangeMaker 3D
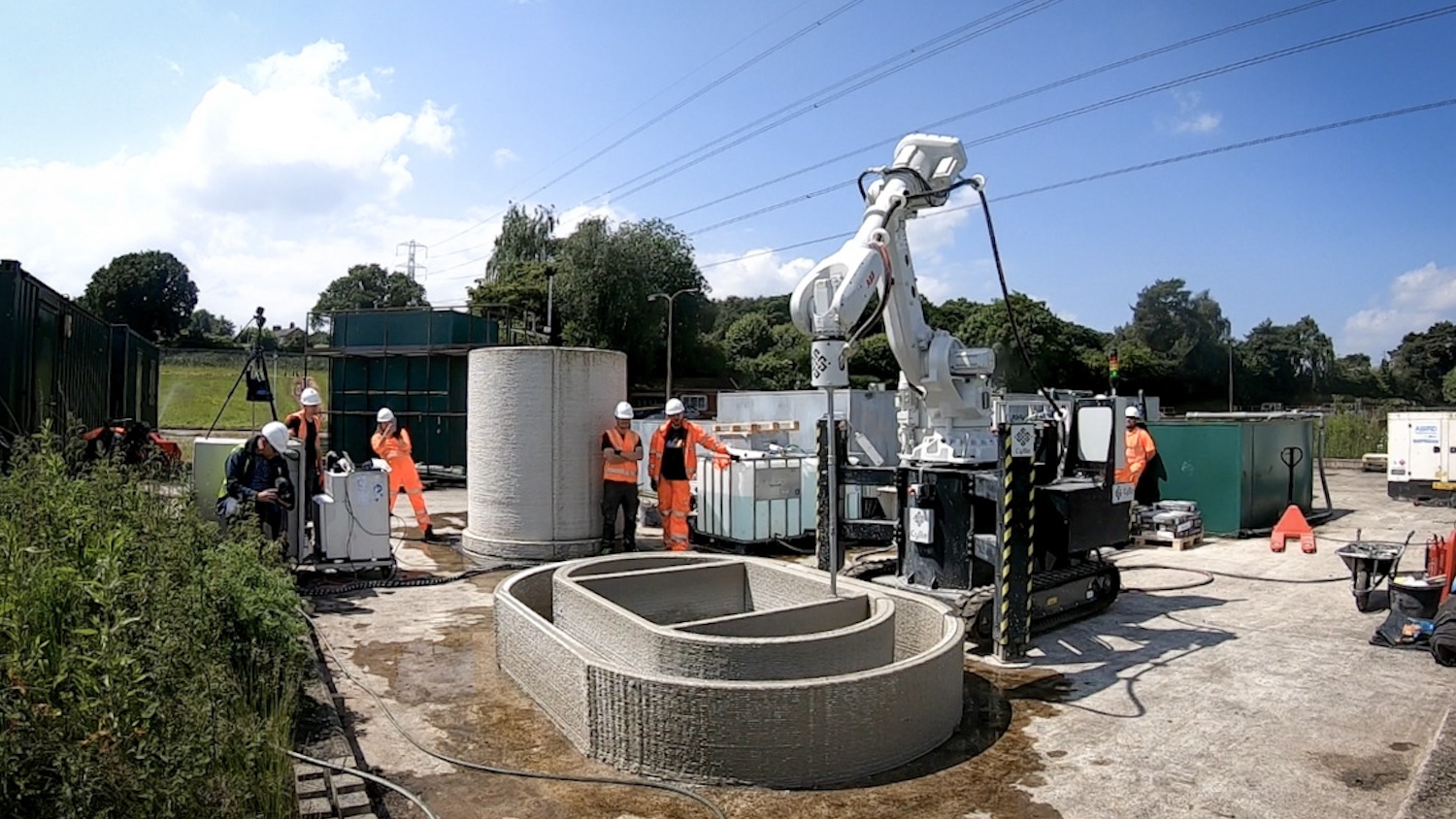
The UK water industry needs to maintain and improve ageing infrastructure while meeting ambitious regulatory and environmental targets. Alternative construction methods that enhance efficiency and sustainability are necessary.
To address this challenge, United Utilities (UU), ChangeMaker 3D (CM3D), Scottish Water and Manchester Metropolitan University secured funding from Ofwat’s Innovation Fund Catalyst Stream for the Water Industry Printfrastructure (WIP) programme. This initiative aimed to explore innovative construction practices to improve and enhance project delivery across the sector.
3D concrete printing technology was identified as a gamechanger, offering rapid, flexible and sustainable asset production. By enabling onsite fabrication, this technology helps mitigate supply chain risks, reduces lead times and delivers critical infrastructure faster and more efficiently.
The WIP programme established the UK’s first 3D concrete printing hub at a live wastewater treatment works hosted by UU. The project also marked several industry firsts, including the first operationalised 3D-printed assets for the water sector, first patented designs and first insitu printing applications.
Implementation involved rigorous planning, research and collaboration. CM3D’s patented designs enabled the production of key assets such as Industrial Emissions Directive (IED) walls, manhole rings and CSO chambers.
Scottish Water installed the UK’s first 3D-printed manhole ring and CSO chamber, demonstrating the technology’s potential for nationwide adoption. Printing infrastructure on site reduced lead times by up to 70% compared to traditional methods.
WholeHouse | Travis Perkins
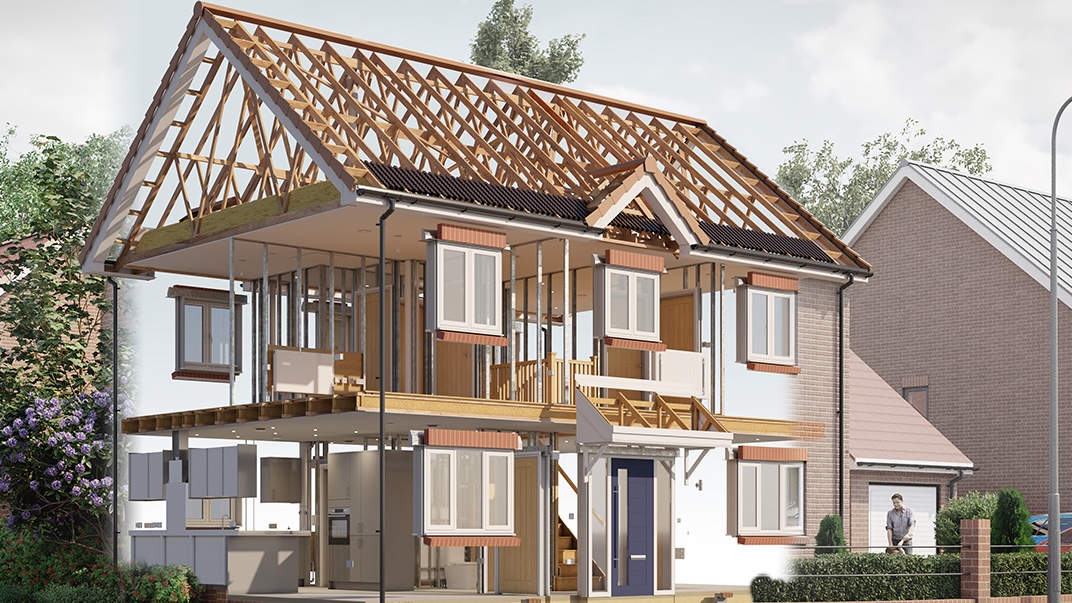
Two years on since first being shortlisted at the Digital Construction Awards, Travis Perkins’ WholeHouse has borne fruit with the first homes delivered by builders using the platform.
WholeHouse was designed to enable housebuilders to configure homes quickly, eliminating inefficiencies while ensuring full regulatory compliance from the outset. The introduction of the upcoming Future Homes Standard, alongside regulations such as Part O and Part S, has made sustainable design and construction more complex. WholeHouse embeds these requirements directly into the design process, ensuring compliance without the need for repeated redesigns.
Additionally, the platform allows housebuilders to integrate renewable energy solutions and measure embodied carbon impact in real-time, supporting net-zero ambitions.
Housebuilders using WholeHouse have already experienced tangible benefits:
- Bowbridge Homes used the platform to improve thermal performance, integrate renewable energy solutions, and streamline onsite practices; and
- Gallion Homes found that WholeHouse eliminated design headaches, providing a fully coordinated, regulation-compliant solution that simplified construction.
The winners will be revealed at the gala dinner on 1 July at the Brewery in London.
The Digital Construction Awards are organised by Digital Construction Week, Construction Management and the Chartered Institute of Building. The first sponsor to be announced is Bluebeam.
View the original article and our Inspiration here
Leave a Reply