This article is one in a series of conversations with women leaders in the construction industry. Click here for past discussions.
Liz Fong didn’t imagine how much technology would play a role in her career when she first enrolled as a sheet metal apprentice 13 years ago.
The operations integration manager at Seattle-based mechanical contractor MacDonald-Miller Facility Solutions said that she envisioned herself carrying out traditional tasks in the field or shop on HVAC or architectural work. She didn’t anticipate the experience she gained in the technological aspects of the industry, including software and technology management, process development and coding.
For her work harnessing construction technology to drive the industry forward, such as helping with her company’s transition to paperless sheet metal fabrication, Fong was recently named the 2025 Innovator of the Year by the Sheet Metal and Air Conditioning Contractors’ National Association.
“Liz is a standout member of our community who is both skilled and proactive,” said Linda Jennings, SMACNA executive director of innovation, integration and learning. “She is a recognized authority on multiple technology platforms and a go-to expert in the field who excels at developing strategies that minimize disruption and maximize results.”
Here, Fong talks with Construction Dive about the work she loves, why she was drawn to a construction career and the importance of technology in the industry.
This interview has been edited for brevity and clarity.
CONSTRUCTION DIVE: What led you to choose construction for your career?
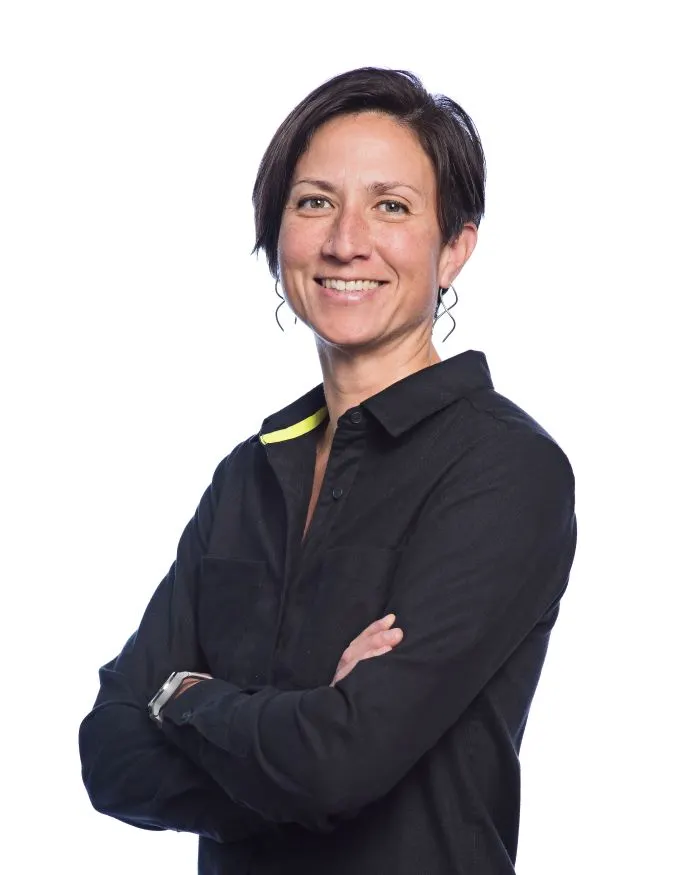
Liz Fong
Permission granted by SMACNA
LIZ FONG: After initially pursuing the college route and eventually continuing to a graduate program, I ultimately decided not to continue down that path. However, I was still looking for a career that would allow me to build something long-term and fulfilling. Additionally, as I approached my 30s, financial security became more of a priority.
That’s when a friend introduced me to Oregon Tradeswomen, where I was first exposed to the trades and the idea of construction as a career. I found the hands-on nature of the work, the diversity of the trades and the potential for growth really appealing.
Equally attractive was the “earn-while-you-learn” structure of apprenticeships and the high floor set by the trade unions, which provide not just steady work but also strong benefits and a clear path for long-term advancement.
The trades and construction seemed like the perfect fit, offering both the stability and variety I was looking for.
Why do you enjoy working in the sheet metal industry specifically?
The diversity of the trades has always appealed to me. When I was first exposed to multiple trades through Oregon Tradeswomen, it was the variety within sheet metal that led me to pursue it over the others.
In the 13 years since, it has not disappointed, though not always in the ways I expected. What I didn’t anticipate was transitioning into software and technology management, process development or coding.
My responsibilities began with managing our model authoring software, which lets users create BIM models, their associated databases and customizations, and have since expanded to influence integrations across the entire lifecycle of model data — spanning the fabrication shop, field operations, logistics and even extending to estimating.
And now, I can’t imagine doing anything else. While I’m no longer hands-on with my tradecraft, it’s a privilege to support my trades family and facilitate their success.
What are some of the projects you’ve most enjoyed working on and why?
A few projects I’ve particularly enjoyed working on stand out due to the sense of trust and responsibility they gave me, as well as the opportunity to develop new skills.
As an apprentice, one project that stands out is the Via6 Towers in Seattle, for which I touched just about every single louver plenum assembly across two 24-story buildings. While far from glamorous, the fabrication process was specific and differed from the traditional duct fabrication I had done up until that point, which made it a special experience for me as a first-year apprentice.
Another memorable project was the Yakama Casino in Toppenish, Washington, which was my first detailing project. It marked a pivotal moment in my career as a springboard into using technology in my work.
This transition allowed me to build on my trade experience while diving into the broader scope of fabrication processes and technical workflows, not just for sheet metal, but also for plumbing and piping trades as well.
On the workflow development side, I really enjoyed contributing to our transition to paperless sheet metal fabrication. This project involved gathering and transforming data for various purposes, from inventory management and material ordering to facilitating specific shop station activities.
It was a great way for me to apply my experience with Autodesk Fabrication content, VDC and shop fabrication workflows, while also exploring new areas like SQL and PowerApps. The project was both a challenge and a rewarding opportunity to expand my skill set while improving our team’s overall efficiency.
What benefits are there to working in construction?
One of the most rewarding aspects of working in construction is the tangible nature of the final product — whether your primary tool is a hammer or a computer. It’s incredibly satisfying to see the direct impact of your efforts on a project, knowing you’ve contributed to building something meaningful.
The work offers variety, requiring a diverse set of roles and skills, and because the industry is always evolving, there’s always something new to learn. This keeps things interesting and helps avoid the monotony found in other fields.
Additionally, construction offers stability. As a union member, I enjoy job security, competitive wages, strong benefits and a clear path for long-term advancement. The “learn while you earn” structure of apprenticeships is also a huge advantage, with a low barrier to entry that makes the trades accessible to people of all ages and backgrounds.
What advice would you give to young women considering construction as a career?
For anyone considering a career in construction, my advice would be to embrace the opportunities the industry offers, even if it feels intimidating at first. Don’t let stereotypes or outdated perceptions hold you back from pursuing the trades or limit your understanding of construction to manual labor.
With the advancement of technology and the increasing emphasis on safety, there’s a place for everyone in every aspect of construction, from the field to the office, and everything in between.
Know that your unique perspective is valuable and vital to the success of any industry. Diversity brings new ideas and approaches, which are critical to innovation and creative problem-solving. The construction industry offers the chance to build a career that is not only personally fulfilling but also provides long-term financial security and growth.
View the original article and our Inspiration here
Leave a Reply